实验机械误差,基于实验误差的机械系统精度评估方法论
概述
实验机械误差是机械系统在实际使用过程中偏离其预期性能的表现。它影响机械系统的精度、可靠性和安全性,是机械系统设计、制造和使用过程中需要考虑的重要因素。
误差来源
实验机械误差通常由以下因素引起:
几何误差:部件的形状、尺寸、位置公差超出允许范围。
运动误差:机械系统运动时产生的偏差,如偏心、间隙、非线性移动。
材料误差:材料特性的变化导致部件性能不一致。
环境误差:温度、湿度、振动等环境因素对机械系统的影响。
操作误差:操作人员的失误或不当操作。
误差评估
实验机械误差的评估是机械系统精度评估的重要一步。常用的评估方法包括:
重复性试验:多次重复相同实验操作,观察测量结果的可重复性。
再现性试验:在不同条件下重复相同实验,比较测量结果的一致性。
校准和溯源:将机械系统与已知精度更高的参考设备进行比较,校正测量误差。
基于实验误差的机械系统精度评估方法论
步骤 1:确定关键误差源
需要根据机械系统的设计和使用条件,识别影响精度最关键的误差源。这可以通过分析设计图纸、进行仿真或进行试验来实现。
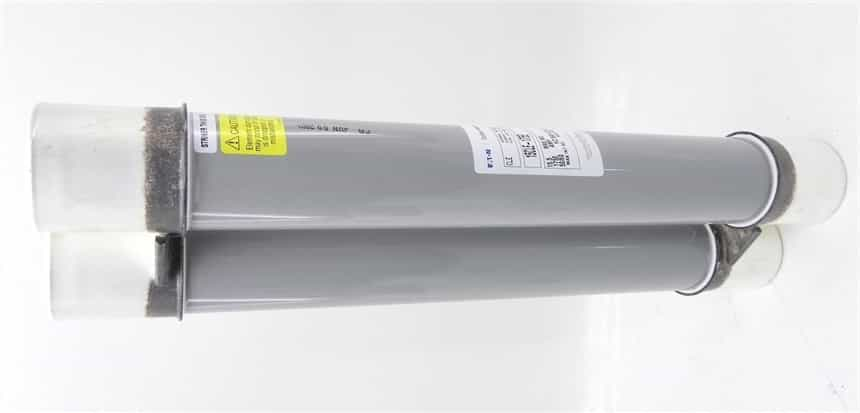
步骤 2:设计和实施实验
设计实验以测量关键误差源的量化值。实验应严格按照标准化程序进行,以最大程度地减少操作和环境误差的影响。
步骤 3:分析和解读数据
收集实验数据后,进行统计分析以确定误差的分布和大小。测量误差通常以标准偏差、公差范围或置信区间等参数表示。
步骤 4:评估精度
基于实验误差的评估,可以确定机械系统的精度指标。常见的精度指标包括:
精度:测量值与真实值之间的最大偏差。
重复性:重复测量值之间的最大偏差。
稳定性:一段时间内测量值的变化量。
步骤 5:改善精度
根据精度评估结果,采取措施改善机械系统的精度。这可能涉及调整设计参数、改进制造工艺或采取补偿措施。
应用
基于实验误差的机械系统精度评估方法论广泛应用于各种机械应用,包括:
机床精度:评估机床的定位和运动精度。
测量仪器精度:校准和评估测量仪器的精度。
机器人精度:评估机器人运动和轨迹规划的精确度。
自动化系统精度:评估自动化系统的整体性能和稳定性。
实验机械误差是影响机械系统精度和可靠性的重要因素。通过基于实验误差的机械系统精度评估方法论,可以定量评估误差来源并采取措施改善系统的性能。该方法论在机械设计、制造和使用过程中具有广泛的应用价值,有助于确保机械系统满足预期要求和安全标准。